
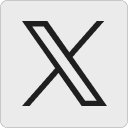


Smart Data is reshaping the Automotive Aftermarket industry, yet most of the organizations are not able to get the expected outcomes from their existing parts catalog and other digital assets. The objective of this innovation is to enhance the output of existing catalogues, Improve Accuracy and reduce parts returns by Enhanced VIN.
A standard VIN contains information about a vehicle including the make of the vehicle, the factory where it was built, and its driveline, engine, transmission and, possibly, the trim level. Where Enhanced VIN data includes codes for the exact trim level and options that the vehicle contains when it rolls off the assembly line. Depending on the automaker, certain high-level information may already be encoded within the VIN. But even with the most forthcoming manufacturers, determining accurate vehicle parts and valuation amid these variables can be challenging.
To address this challenge, one of the most innovative technologies to come out in the automotive industry in recent times, The API simplifies identification of car parts by enhanced VIN data. Just enter VIN or LP or scan from the phone’s camera and access the complete universe of data about that particular vehicle in just a tap on the screen. Let’s dive deep into this innovation and evaluate its effectiveness by comparing the traditional and smart way of parts cataloging.
The Traditional Way of Parts Cataloging –

The automotive aftermarket industry has been witnessing challenges before, and not just this ongoing crisis. The solution majorly includes technology innovations. Although the industry has embraced IT, there is still a long way to go to maximize potentials. The problem begins with being able to Identify the right make – model – variant – year – type and eventually the trim of the vehicle. This renders multiple options of replacements parts and makes it difficult to choose from. Majority of the aftermarket parts catalog in the EU countries is based on after-market supplier data sets aggregated by multiple data consortiums or aggregation groups. These are usually mapped to vehicle classifiers and parts categories defined by these groups. The current web catalogues work on the license plate, the LP is entered into the system which is then deciphered to a classifier ID which in turn is mapped to a category ID for creating a parts tree – but all this is usually driven by classification on the make – model – variant – year and type in. This would never consider the impact of the trim or the optional equipment or features installed on the vehicle during production.
The Smart Way of Parts Cataloging –
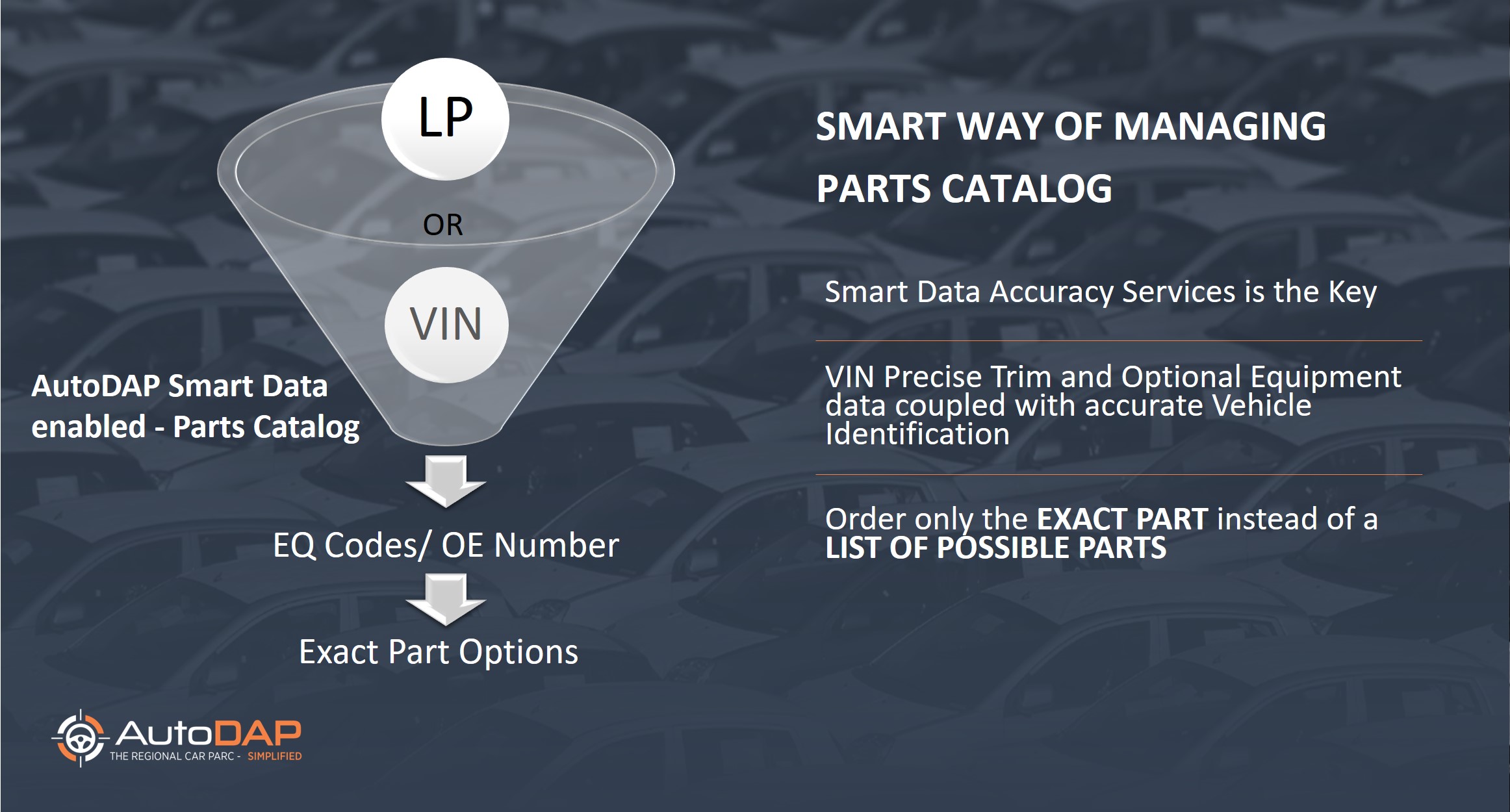
As mentioned above the Parts manufacturers’ data is based on vehicle type and not the actual configuration of the vehicle, hence the precise vehicle identification mapped to vehicle configuration is very critical. This renders a list of possible parts and not the exact suitable part for the specific vehicle.
The AutoDAP Data as a Service platform can be seamlessly integrated with existing catalog solutions. The search methodology of the catalog can be expanded with searching by License plate or VIN in order to go to the detailed trim level of that specific vehicle. With this information based on the manufacturers build sheet, detailed information about the specifications of the vehicle, or installed parts can be collected and implemented into the catalog, refining the output of the current catalog system. In cases where multiple parts are in the catalog, through a mapping on the EQ codes provided in the build sheet the suitable part can be high lighted or non-suitable parts stay hidden in the web interface.
Non-relevant data is often the reason why over-ordering occurs. By filtering the catalog data with DaaS output makes it possible to get the accurate parts first time right. It can reduce the parts returns for the parts seller. It has also covered OE based parts identification for the white spots of unavailable vehicle parts.
Product management can start looking for supplier matched based on the OE number. The gaps in the catalog can be covered quite fast with this additional information. So, it’s not only upgrading the part catalog accuracy but also delivers information towards product management on new cars or white spots at existing cars increasing the product coverage to market.
The DaaS module helps to determine the correct part more easily for the mechanic, it reduces the time needed to search the part and can also make it possible to order the part before the customer is in the workshop with the vehicle. On the parts distributor side, this results in fewer returns due to the fact over-ordering is not needed by the mechanic, and fewer handling and repacking costs. This can also have a positive impact on the inventory stock levels for the retailers.
The higher “first-time-right” means also for the customer a higher guarantee that the car is ready on the same day. Even certain jobs can be done with the customer waiting instead of utilizing a courtesy/loan car. So it seems like a win-win situation for the parts suppliers, the mechanics and car owners too.
Conclusively, the benefits of using DZAS modules to smarten up the parts catalog are –
- Increased First-time right Parts
- Reduced Returns and logistic handling efforts
- Improved Turnaround Time
- Increase in operational efficiency
- Customer Delight or user journey of the application will come to a higher level of accuracy
The impact is not just on the ordering process but overall operational efficiency, which is critical for sustained competitive advantage. Some of our customers have witnessed 75-80% reduction in parts returns with a direct impact on the cost reduction and improvement in the bottom line.
Are you looking forward to enhancing the output of existing catalogs, Improve Accuracy, Reduce parts returns to achieve operational efficiency, improved bottomline and sustained competitive advantage?
Get free assessment and demo of AutoDAP DaaS modules by contacting us at marketing@autodap.parts